7% of global CO₂ emissions can be traced back to the use of concrete withinthe construction industry.
It’s time to rethink and innovate.
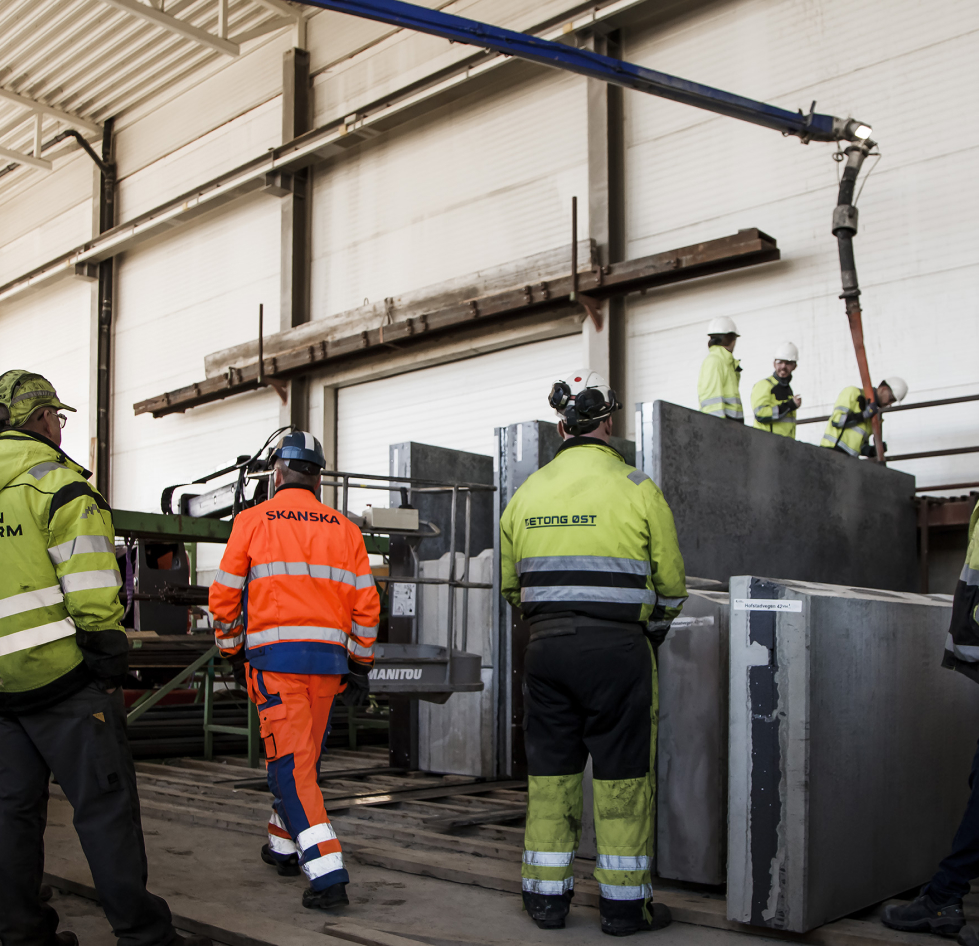
Tons of surplus wood is thrown away in Norway every year
Of CO₂ emissions is released from burning this wood
M³ of concrete is used in Norway a year
Of global CO₂ emissions stem from concrete worldwide.
Consider the environmental impact of traditional concrete: a whopping 7% of global CO₂ emissions stem from its use in the construction industry.
Now, envision a different approach.
Enter Biocrete – a concrete innovation that addresses climate concerns. By utilizing wood waste from the building sector, Biocrete presents a potential solution. As Norway aims to honor the Paris Agreement, and cut CO₂ emissions by half by 2030, sustainable alternatives are imperative. Biocrete isn’t not just a material; it's a significant step towards a greener construction industry.
Biocrete contributes to solving the challenges of emissions, waste, and supports the emerging biochar industry in Norway. It's a quiet revolution in the world of construction, working towards a more sustainable future.
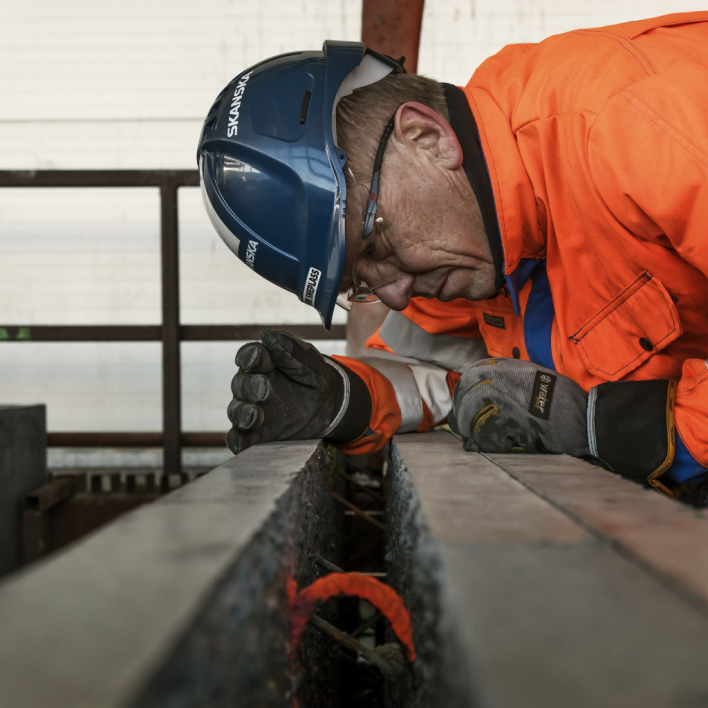
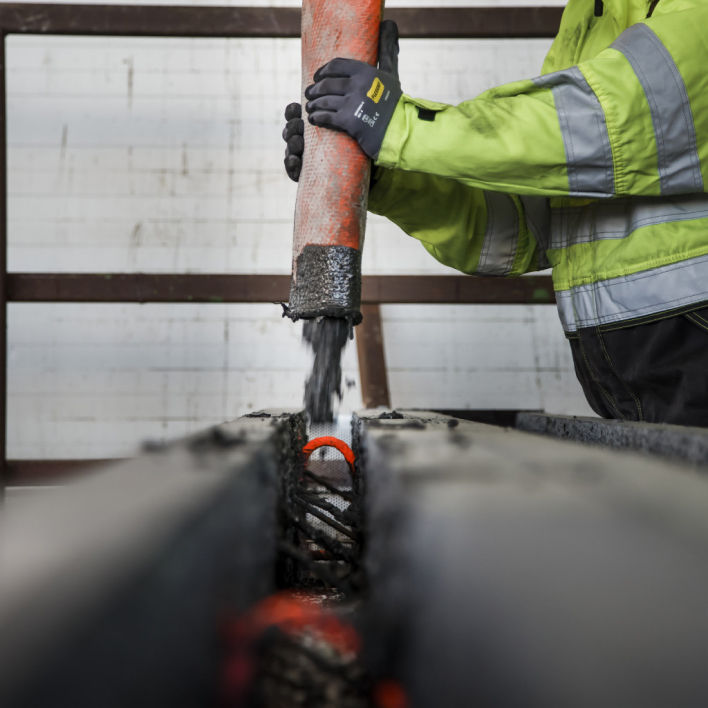
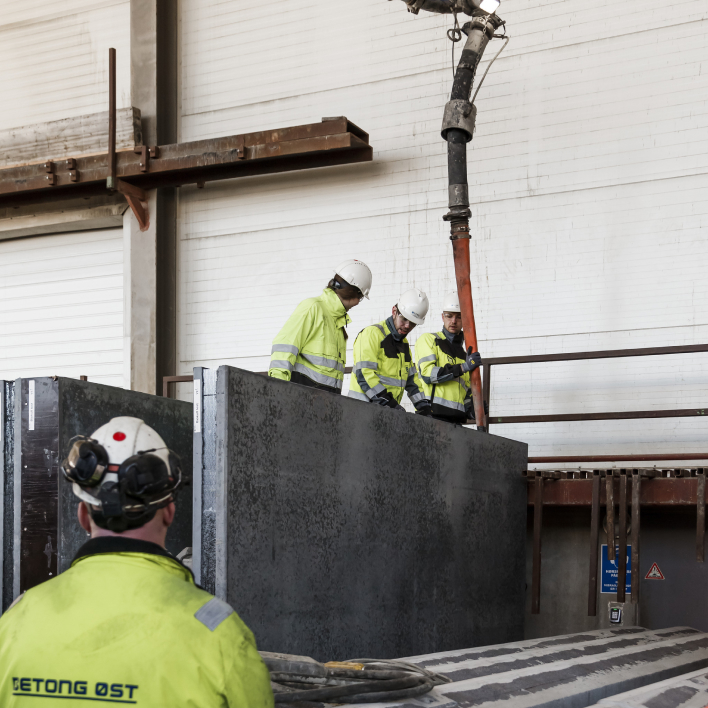
Proven to be carbon-neutral or even carbon-negative, Biocrete is a building element that can help you build a more sustainable future
Norway discards a staggering 1 million tons of wood waste annually, emitting1.8 million tons of CO₂ into the atmosphere. Our solution? Pyrolyze this wood waste from construction sites to create biochar.
Harnessing excess heat for district heating, we mix the biochar with over 90% carbon into the concrete, offsetting emissions from production, transport, and rebar.
The result? A carbon-neutral product with lasting benefits—each kilo of carbon in our concrete saves 3.67 kg of CO₂. This is carbon storage, a game-changer in climate solutions.
Our full-scale tests, conducted with Con-Forms, Betong Øst, and NTNU, proved the practicality, strength, and carbon negativity of our concrete elements. Biochar not only compensates for concrete emissions but also offsets the impact of reinforcing steel.
Søndre Haneborg Gård
A Biocrete barn
In June 2023, we initiated the Biocrete casting process in a pilot building situated at Søndre Haneborg, just outside Oslo.
Søndre Haneborg Gård, an agricultural barn, aspires to be the most environmentally friendly barn ever constructed in Norway. This 1200m2 barn combines concrete and CLT in its construction. The ground floor and subterranean structures consist of a mix of Low Carbon Class A and Biocrete, sourced from Betong Øst and Con-Form.
The walls were constructed with precast sandwich elements from Con-Form, filled on-site with Biocrete using a tub. The slab construction involves prefabricated elements reinforced on-site and fully cast with Biocrete, with a steel-smoothed top surface. Despite minor issues with one of the delivery trucks, the process unfolded seamlessly, resulting in a highly satisfactory outcome.
Through this pilot, we achieved an emission reduction of 11,664 kg of CO2, locking it into the Biocrete.
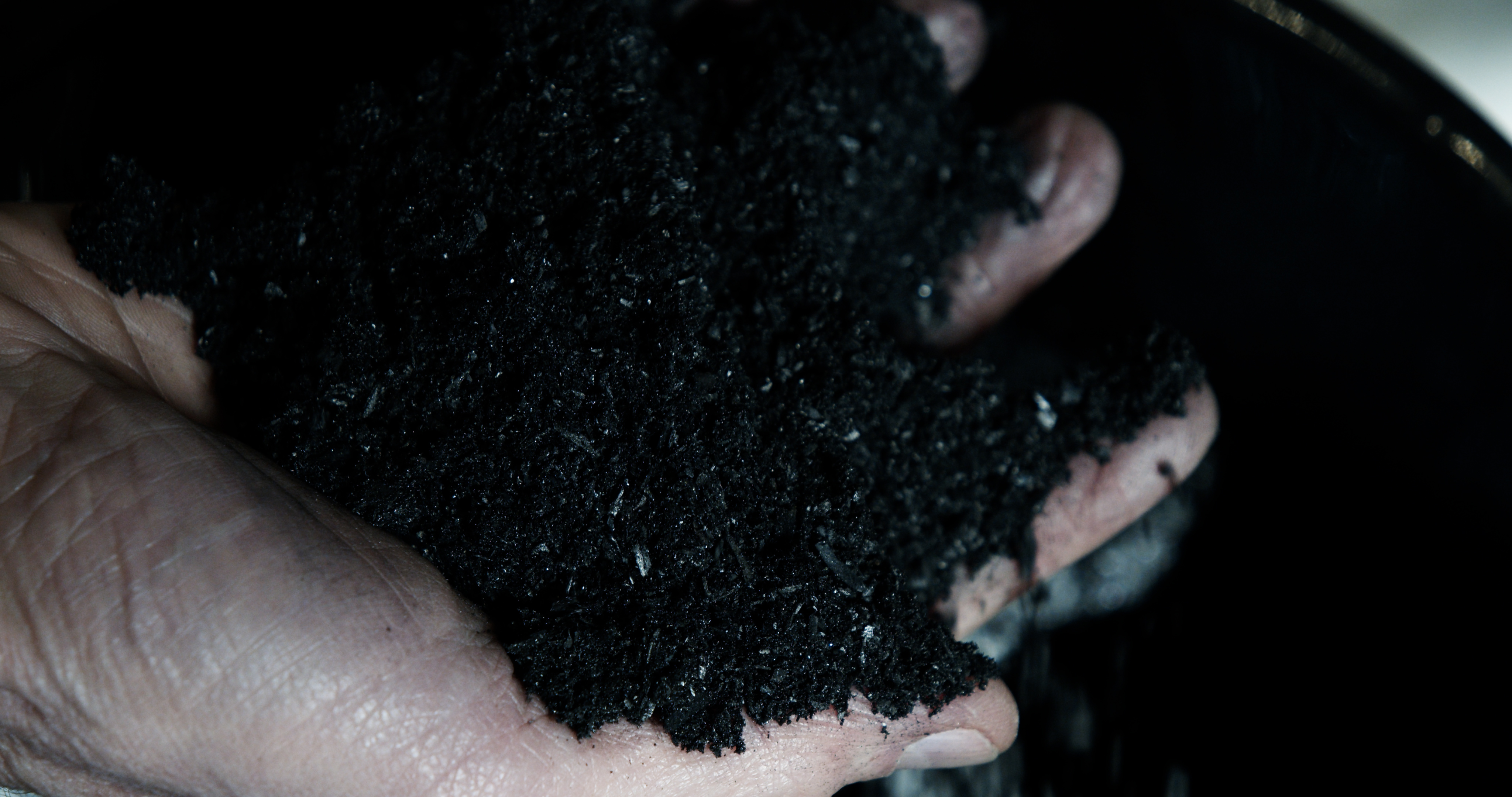